Comprehending the Secret Parts and Repair Strategies for Product Packaging Equipment Maintenance
Effective maintenance of product packaging equipments pivots on a complete understanding of their key elements, consisting of the structure, drive system, and securing devices. Recognizing usual maintenance problems, combined with the implementation of preventative methods and fixing methods, can dramatically enhance device dependability.
Trick Components of Product Packaging Equipments
Product packaging machines include several key parts that interact to ensure efficient and effective product packaging procedures. At the core of these equipments is the structure, which gives structural integrity and houses the various operating parts. The drive system, typically a mix of motors and equipments, facilitates the activity of parts, making it possible for specific procedure throughout the product packaging cycle.
An additional crucial part is the conveyor system, which delivers items with various stages of the packaging procedure. This is often enhanced by sensing units and controls that check the placement and rate of products, making sure synchronization and lessening mistakes. The loading system is important for precisely dispensing the right amount of item into packages, whether in fluid, powder, or solid form.
Securing systems, including heat sealants or sticky applicators, play an important role in safeguarding plans, protecting against contamination and prolonging life span. In addition, identifying systems are integral for giving necessary item information, making certain compliance with laws. Lastly, the control panel, equipped with easy to use interfaces, enables drivers to handle machine features, monitor performance, and make changes as needed, making sure ideal efficiency and performance in packaging procedures.
Common Upkeep Concerns
Efficient procedure of packaging equipments counts greatly on routine maintenance to avoid usual concerns that can interfere with manufacturing. Among these concerns, mechanical deterioration prevails, particularly in elements like conveyors, electric motors, and seals, which can lead to unforeseen downtimes. Additionally, imbalance of parts can result in ineffective procedure, creating products to be improperly packaged or harmed throughout the procedure.
One more typical maintenance problem involves the build-up of dirt and particles, which can disrupt the maker's sensors and relocating parts. packaging machine repair service. This not only affects performance however can likewise position safety and security threats. Lubrication failures can lead to raised rubbing, resulting in getting too hot and eventual part failing.
Electrical issues, commonly stemming from loosened links or damaged circuitry, can interrupt equipment functions, resulting in significant manufacturing delays. Last but not least, software application glitches because of improper arrangements or outdated programs can prevent the equipment's procedure, necessitating instant treatment. Dealing with these common maintenance problems proactively is necessary for ensuring optimal performance and durability of packaging equipment.
Preventative Maintenance Approaches
Applying preventative upkeep techniques is essential for sustaining the effectiveness and reliability of packaging makers. These approaches encompass a systematic method to upkeep, concentrating on the regular assessment and maintenance of devices to preempt prospective failures. By adhering to a scheduled maintenance program, drivers can determine damage on parts prior to they result in substantial failures.
Crucial element of a preventative maintenance approach include regular assessments, cleaning, component, and lubrication substitutes based upon producer recommendations. Utilizing lists can streamline this process, guaranteeing that no vital tasks are ignored. Furthermore, preserving exact records of maintenance activities aids in tracking the machine's efficiency over time, facilitating informed decision-making pertaining to future upkeep requirements.
Educating team on the significance of preventative maintenance boosts conformity and promotes a culture of aggressive care. Executing a predictive upkeep component, utilizing data analytics and sensor technology, can further maximize equipment performance by predicting failings before they take place.
Fixing Methods
When faced with breakdowns or ineffectiveness in product packaging devices, using organized troubleshooting methods is crucial for recognizing and fixing problems quickly. The very first step in efficient troubleshooting is to establish a clear understanding of the machine's operational specifications and performance metrics. This entails assessing the device's requirements, as well as any mistake alerts or codes shown.
Following, drivers must carry out an aesthetic inspection, inspecting for obvious indicators of imbalance, wear, or damage. This usually consists of analyzing sensing units, Extra resources belts, and gears to pinpoint possible root causes of malfunction. Collecting functional data, such as production prices and downtime logs, can additionally offer insights right into persisting concerns.
Once potential issues are recognized, utilizing a sensible method to separate the origin reason is important. This might need screening specific components or systems in a controlled manner. Taking part in conversations with operators who connect with the equipment frequently can produce beneficial responses regarding uncommon actions or patterns.

Repair Service and Replacement Finest Practices
An extensive understanding of repair service and substitute best methods is vital for preserving the durability and efficiency of product packaging makers. On a regular basis examining the condition of machine parts enables timely intervention, avoiding more substantial concerns that can result in pricey downtimes.
When repair services are required, it is essential to use OEM (Original Equipment Manufacturer) components to guarantee compatibility and efficiency. This my blog not only protects the integrity of the maker but additionally supports service warranty contracts. In addition, it is recommended to keep an inventory of critical extra components to help with fast replacements and reduce functional interruptions.
For complex repair services, engaging licensed technicians with specialized training in packaging equipment is advised. They possess the proficiency to identify concerns properly and perform repair services successfully. Additionally, recording all repair work tasks and components substitutes is essential for preserving a thorough maintenance history, which can help in future troubleshooting.
Last but not least, executing a proactive approach, including normal examinations and predictive upkeep methods, boosts the dependability of packaging devices. By sticking to these ideal techniques, businesses can make sure ideal maker performance, decrease operational risks, and expand devices life expectancy.
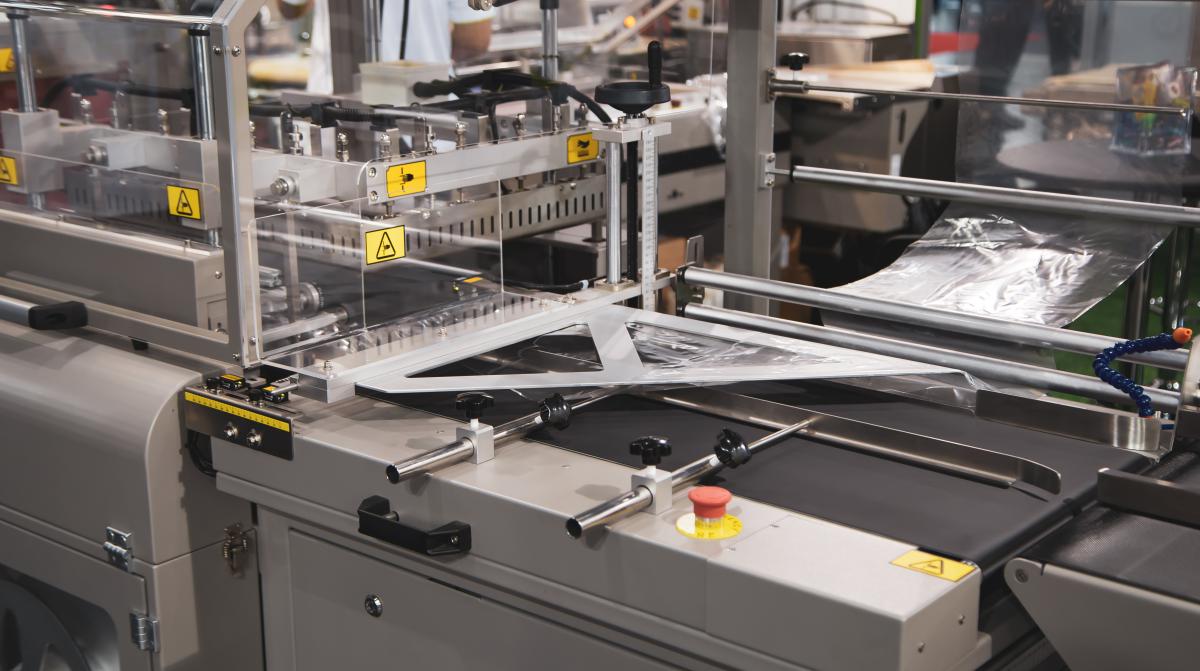
Conclusion
In conclusion, an extensive understanding of product packaging maker elements and reliable upkeep strategies is important for optimal performance. By carrying out these techniques, companies can ensure the durability and effectiveness of product packaging makers, inevitably adding to boosted functional productivity and reduced costs (packaging machine repair service).
Effective maintenance of packaging devices hinges on an extensive understanding of their crucial parts, consisting of the framework, drive system, and securing systems.Efficient operation of packaging devices depends heavily on regular maintenance to protect against usual concerns that can interfere with manufacturing.Carrying out preventative maintenance methods is essential for maintaining the effectiveness and dependability of packaging machines. Furthermore, preserving accurate documents of upkeep activities aids in tracking the equipment's efficiency over time, promoting educated decision-making relating to future maintenance needs.
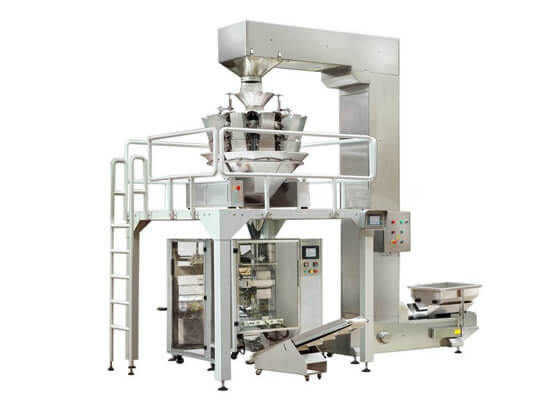
Comments on “Packaging Machine Repair Service for All Brands and Designs of Devices”